Enhancing Results: Casting Aluminum Like a Pro
Enhancing Results: Casting Aluminum Like a Pro
Blog Article
Opening the Possible of Aluminum Spreading: A Comprehensive Summary
Light weight aluminum casting stands as a foundation in the world of metalworking, providing a plethora of benefits and applications throughout various sectors. From its historical value to the modern developments in casting strategies, aluminum has continually proven itself as a useful and flexible product. As we navigate through the landscape of aluminum casting procedures and explore the complexities of top quality control procedures, a comprehensive review of opening the true possibility of this metal arises. The possibilities appear countless, promising insights that can revolutionize the way we use and regard aluminum in production (casting aluminum).
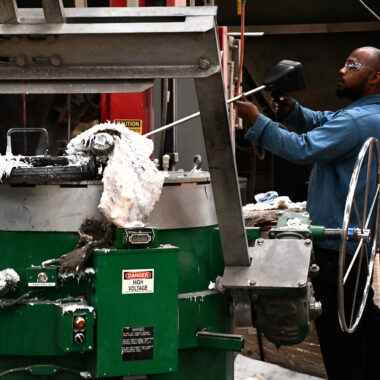
History of Aluminum Casting
Light weight aluminum spreading has an abundant historic history that goes back to ancient human beings, showcasing the withstanding value of this metallurgical process in various markets. The origins of aluminum casting can be traced to about 5,000 B.C. when ancient worlds like the Egyptians and the Sumerians made use of fundamental techniques to cast little items. It was not till the 19th century that aluminum casting saw significant advancements with the exploration of the Hall-Héroult procedure for removing light weight aluminum from its ore, making it much more obtainable for casting functions.
The flexibility of light weight aluminum casting allowed for complex shapes and complex layouts to be produced with accuracy, better sustaining its fostering throughout different sectors. Today, light weight aluminum spreading continues to be a cornerstone in the manufacturing of a broad range of products, highlighting its long-lasting tradition and value in contemporary manufacturing procedures.
Benefits and Applications
With its extraordinary strength-to-weight proportion and excellent thermal conductivity, light weight aluminum casting uses a myriad of benefits and diverse applications across different industries. One of the primary benefits of aluminum spreading is its lightweight nature, making it an optimal choice for sectors where weight reduction is vital, such as vehicle and aerospace.
In regards to applications, light weight aluminum casting is extensively used in the vehicle market for parts like engine blocks, cyndrical tube heads, and wheels as a result of its toughness and light-weight residential or commercial properties. The building and construction sector take advantage of light weight aluminum spreading in the manufacturing of decorative elements and structural elements. The versatility of light weight aluminum spreading extends to customer electronics, where it is used in the manufacturing of coverings and heat sinks. On the whole, the advantages of light weight aluminum spreading incorporated with its varied applications make it an essential material in various industrial industries.
Sorts Of Aluminum Spreading Procedures
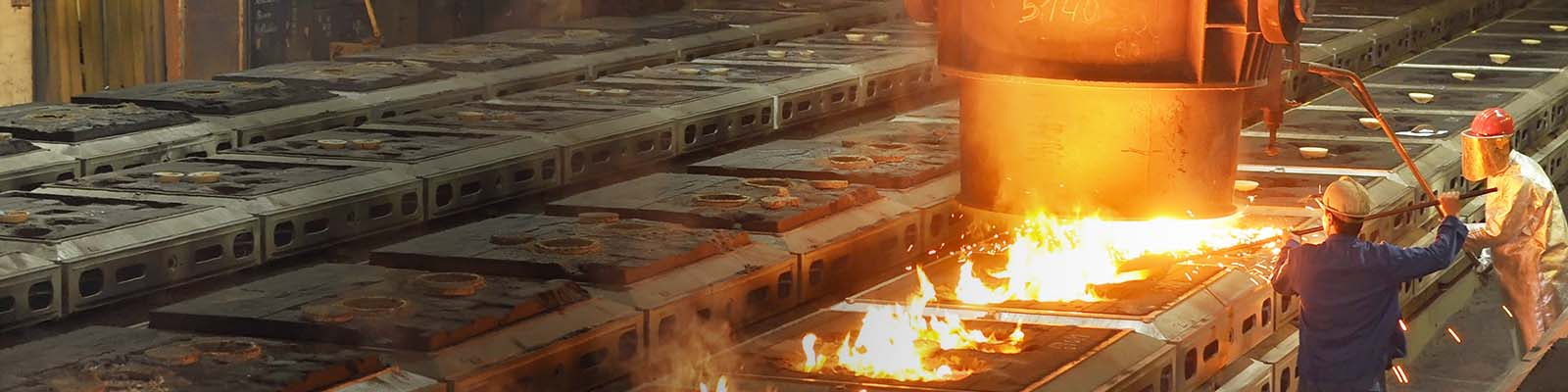
Amongst the different techniques used in industrial setups, aluminum casting procedures encompass a variety of techniques fit to various applications and demands. Among one of the most common approaches is sand spreading, where a mold and mildew is produced by compacting sand around a pattern of the desired component. This process is affordable and flexible, making it prominent for both little and large-scale production. An additional widely made use of technique is pass away casting, which involves compeling molten light weight aluminum right into a mold and mildew cavity under high stress. Die casting enables high precision and repeatability, making it suitable for creating complicated forms with thin wall surfaces. Investment casting, additionally referred to as lost-wax casting, is preferred for its ability to create thorough and complex parts with a smooth surface area finish. Finally, long-term mold spreading includes making use of recyclable steel mold and mildews to develop constant and high-grade aluminum components. Each of these light weight aluminum casting look at this web-site procedures provides distinct benefits, dealing with a variety of industrial requirements.
Developments in Light Weight Aluminum Spreading Techniques
Recent innovations in aluminum casting methods have actually revolutionized the manufacturing market, supplying improved efficiency and precision in the manufacturing of facility parts. One notable development is the advancement of 3D sand printing modern technology, which enables the creation of elaborate sand molds with very little manual work. This strategy permits better design flexibility and faster production cycles, making it perfect for prototyping and little batch production.
Additionally, using sophisticated simulation software program has actually dramatically boosted the spreading procedure by making it possible for designers to enhance mold and mildew styles and anticipate prospective problems before production starts (casting aluminum). This causes boosted item high quality and minimized product waste
In addition, the fostering of vacuum-assisted aluminum casting has boosted the total top quality of castings by reducing porosity and guaranteeing a more consistent circulation of molten metal. This strategy is specifically helpful for elements that require high architectural stability and exceptional surface coating.
Quality Assurance in Aluminum Spreading
The improvements in aluminum spreading methods have not only boosted effectiveness and precision yet have also emphasized the vital importance of quality assurance in making sure the reliability and efficiency of cast parts. Quality control in light weight aluminum spreading involves a methodical approach to examine the production and check process, recognizing any type of inconsistencies from set criteria that might influence the end product.
One essential facet of quality control is the usage of advanced innovations such as non-destructive screening methods like X-ray and ultrasound to identify internal flaws without compromising the stability of the actors components. Additionally, carrying out rigorous evaluation methods at various stages of production aids in identifying and correcting problems without delay, guaranteeing that only parts fulfilling the defined criteria are released for usage.
In addition, quality assurance extends beyond the production procedure to incorporate post-casting procedures like heat treatment and surface completing, ensuring that the end products fulfill the wanted specifications. By prioritizing quality control steps, makers can boost item uniformity, longevity, and overall customer complete satisfaction in the realm of aluminum casting.
Final Thought
Finally, aluminum casting has a rich history and offers numerous advantages and applications across numerous sectors. Various sorts of casting procedures and ingenious methods have been developed to enhance the efficiency and top quality of light weight aluminum spreading. Quality control steps play an important function in guaranteeing the final items satisfy the called for criteria. Generally, aluminum casting remains to be a beneficial production process with great possible for more improvements in the future.
As we navigate navigate to this website via the landscape of aluminum spreading processes and dive into the intricacies of high quality control measures, a thorough summary of opening the true possibility of this metal arises. It was not until the 19th century that light weight aluminum casting saw considerable advancements with the exploration of the Hall-Héroult process for drawing out light weight aluminum from its ore, making it much more obtainable for casting functions.
Amongst the various techniques used in industrial setups, light weight aluminum casting procedures incorporate a range of methods matched to different applications and demands. Financial investment casting, likewise recognized as lost-wax casting, is favored for More Bonuses its capability to generate detailed and elaborate components with a smooth surface area coating. Different types of casting procedures and cutting-edge techniques have been established to improve the performance and quality of aluminum casting.
Report this page